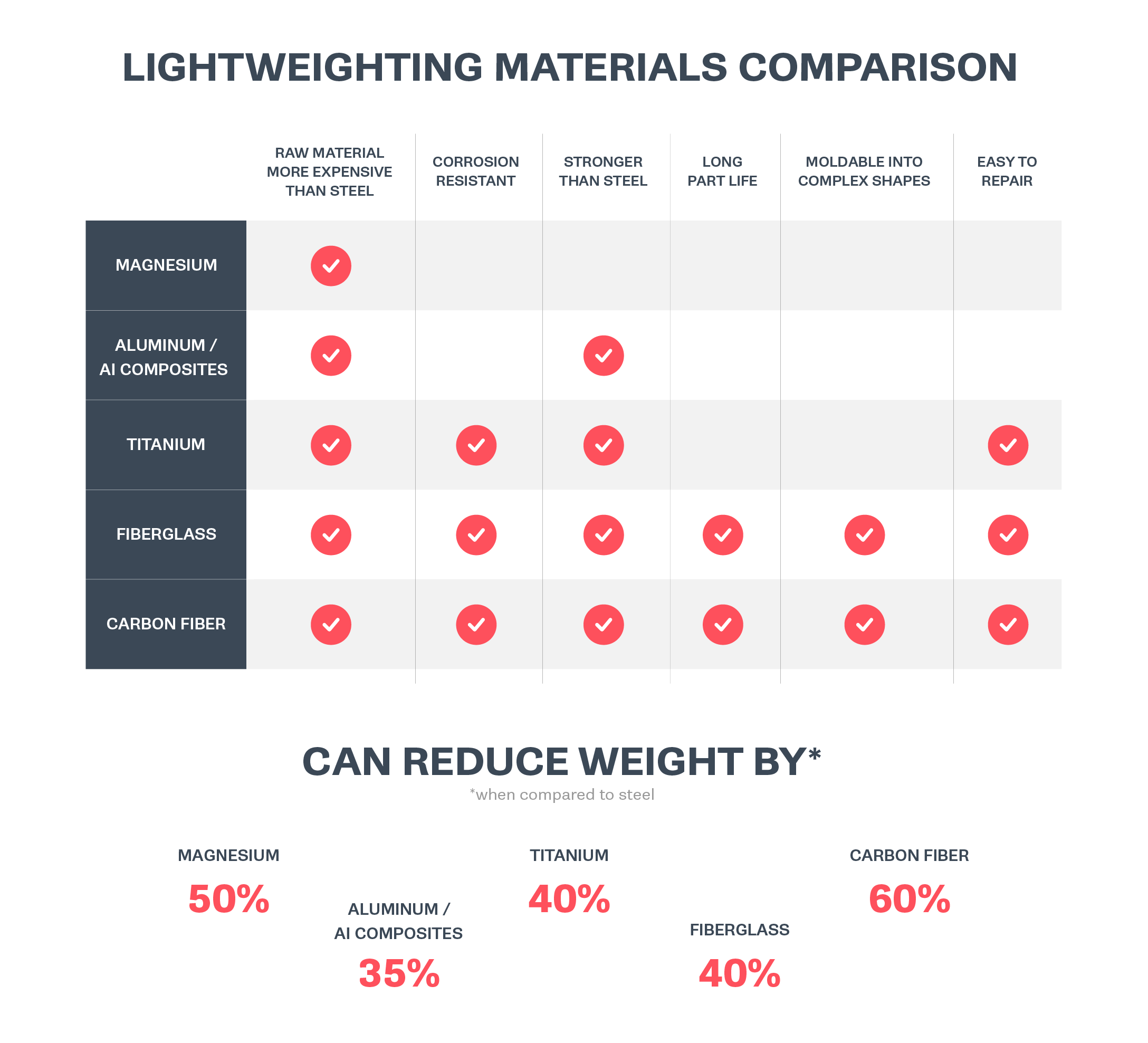
Reduction of Weight
The automotive industry is trending towards lighter-weight cars for many reasons:
- The lighter a car is, the more energy-efficient it is. Without sacrificing performance or safety, materials used to lightweight cars can help improve the fuel efficiency of a car. This is especially important with hybrid or electric vehicles, as these batteries can be very heavy.
- Lightweight cars improve performance. When a car is lighter, it becomes easier to maneuver, making it easier (and more fun) to drive.
- Lightweight materials increase passenger safety. Driving in poor conditions in a heavy car can be dangerous because of the car’s momentum – a heavier car means less agility, even when you need it most. Additionally, materials used to lightweight cars are typically stronger than steel and can absorb energy better, meaning in the case of a collision, energy is less likely to be transferred to the cabin.
Something to consider: the lighter a car, the more these structures will radiate noise, creating an uncomfortable, or even dangerous passenger experience. When using a material for the purpose of lightweighting a car, it is important to think about how you will account for this increase in noise and vibration.
Cost of Materials
While the cost of these materials is higher than steel, the respective benefits can often help to outweigh the cost. First, it is important to note that raw material cost must be weighed with fabrication complexity and touch labor cost to understand total price. And, consumers will often be willing to pay a higher price for a safer car with better performance and higher fuel efficiency.
Corrosion-Resistance
According to the NACE International IMPACT study, corrosion contributes to $2.5 trillion, or 3.4% of global GDP. This is due to part failure, replacement, and most commonly, product recalls. Corrosion usually occurs when metals come into contact with moisture, therefore replacing these parts that are typically made out of metal with composite materials like carbon fiber greatly reduces the risk of corrosion.
Strength of Material
Historically, steel was used in automotive manufacturing because of how strong it is. While steel is very strong, it derives much of its strength from its weight. Composite materials offer increased strength with less weight required, making them near optimal alternatives to steel.
Life of Material
The life of the material used in automotive manufacturing can be determined by a few factors. Corrosion, as already discussed, is an issue many manufacturers face, and one that will shorten the life of a part. Additionally, fatigue resistance is something that must be considered when manufacturing car parts, as materials with higher fatigue resistance offer a longer life. Of course, a longer part life means less repair and replacing for the manufacturer, as well as higher customer satisfaction.
Ease of Fabrication and Repair
When it comes to fabricating and repairing automotive parts, the material used to manufacture those parts has a big impact on how easy it is to construct and repair. Many composites, such as fiberglass and carbon fiber reinforced materials, can easily be molded into complex shapes without expensive tooling and many body-shops already use polymer-based compounds for repair today. Oftentimes, if a material is too difficult to repair, manufacturers may be forced to completely replace it when required, affecting life-cycle costs.