How Improved Vibration Damping Can Keep Your Manufacturing Ahead of the Competition
The aerospace industry is constantly looking to move forward—pushing the limits to improve speed, range and comfort for all aircrafts in production. In order to stand out, aerospace manufacturers need to take advantage of every new technology at their disposal that may have a positive impact in one or more of those areas.
These technology improvements can include the materials aerospace manufacturers use in their production process. Traditional metallic materials have historically been used heavily in aircraft manufacturing, but new vibration damping composite materials are becoming more and more prevalent in the industry, as they are able to solve many of the problems that aerospace manufacturers are facing and improve the performance and quality of the parts that use vibration damping composite materials.
Defining and Predicting the Market’s Trends
An ongoing trend in aerospace manufacturing is the desire to optimize comfort for the passengers. A 2019 J.D. Power travel survey found that passengers were more satisfied than ever with their experiences with airlines; however, the main area in which passengers were not satisfied was in-flight experience.
No longer a luxury, a comfortable flying experience is a necessity for passengers these days and can mean the difference between flying with an airline that works with one aerospace manufacturer and switching to a different option for a more comfortable experience.
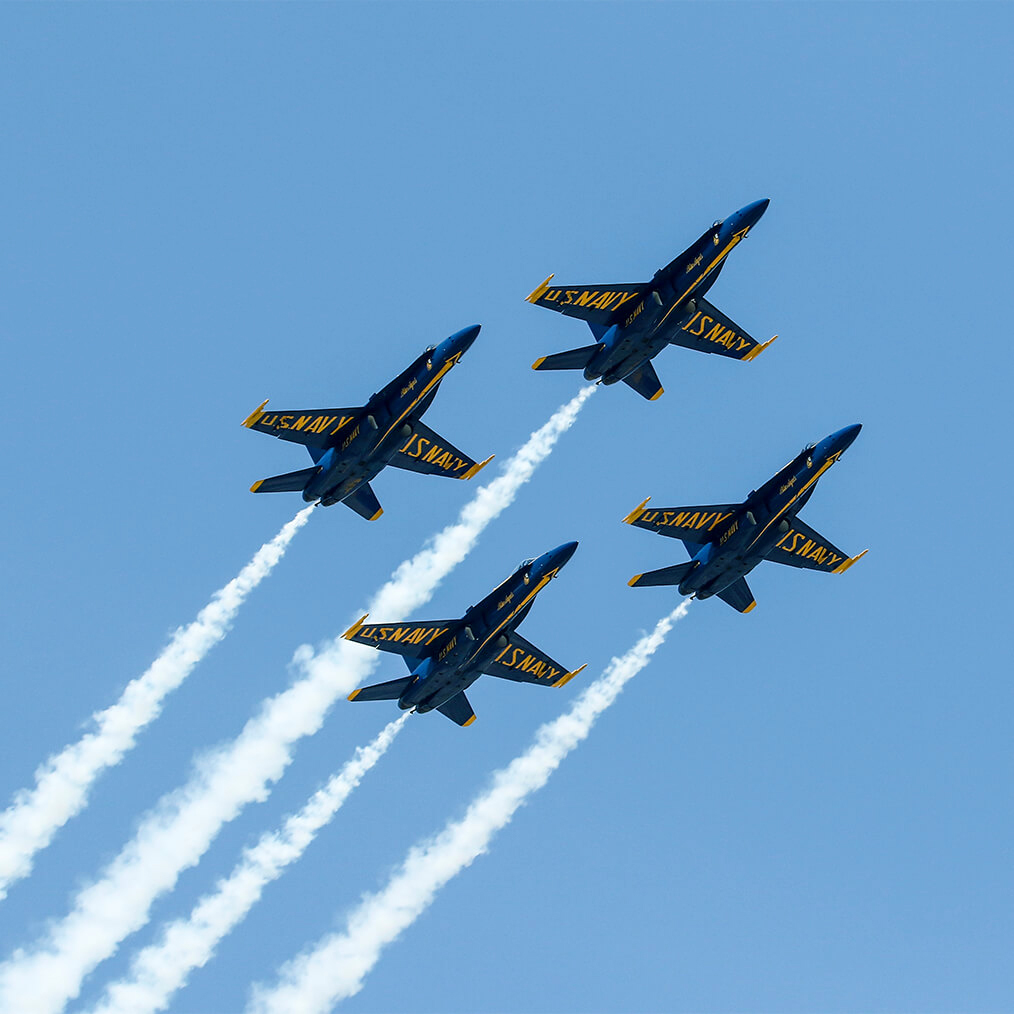
Among aerospace manufacturers, there is a desire for lower weight and higher temperature resistance in order to increase fuel efficiency. In recent years, airlines have worked to create longer and longer nonstop flights, consistently pushing the limits of their aircraft’s capabilities. Singapore Airlines recently created a nonstop flight route from Singapore to Newark, New Jersey, a nearly 19-hour journey, and the five longest nonstop flight paths were all created in the last five years, each of which can last more than 17 hours in the air. With a combination of currently stable low fuel costs, technology innovations and the demand for nonstop flights, this trend only looks to expand beyond what is currently available.
The commercial aerospace sector as a whole has declined in deliveries recently; however, two segments of the market are on the rise. According to a 2019 Deloitte study, military budgets and expenditures worldwide are increasing. A predicted 3 to 4-percent spending growth in the next year means further investment, specifically in the defense aircraft segment, is expected, especially with the variety of products produced for militaries, including helicopters, drones and other military aircrafts. Companies have also been experimenting with the use of drones in non-military capacities, including long-haul logistics.
Another market segment that is projected to see a boost is the regional jet. While the commercial aircraft segment is declining, the demand for regional jets is increasing. The majority of regional jets currently in use are older and smaller, so there is a demand for improved technology and increased size (from about 50 seats per plane to about 70). Worldwide, an aging has led to a predicted demand for more than 5,000 regional jets over the next 20 years, as well as increased expansion for regional connectivity in Asia, South America and the Middle East.
Innovating Beyond Traditional Approaches
The desire to maintain the status quo is a common challenge in the aerospace industry. According to Deloitte, between 25 and 50 percent of aerospace and defense companies have stuck to their traditional strategies and business models despite changes in the industry environment, structure and market needs—and these companies exhibited poorer performance than those that had adapted to the changing environment. The desire for innovation may still be present, but many manufacturers are resistant to adopting new technologies, both on the shop floor and in the physical technologies that are used in their aircraft.
A primary area in which legacy aircraft manufacturers can adapt to the modern manufacturing process is in the materials they use. Two materials are predominantly used in modern aerospace manufacturing: aluminum alloys and composites. Aluminum has been the material of choice for manufacturing aircraft since the beginning of the industry more than 100 years ago— its lightweight, low cost and strong, and a proven method for constructing airframes and skins.
Today, however, some new jet designs use as little as 20 percent aluminum, dropping the material in favor of lighter weight composite materials. The same transition, from traditional metallic materials to composites, is occurring in automotive manufacturing to reduce noise and vibrations, improve component integrity, increase service life and increase battery longevity in electric vehicles.
The development of composite materials in the 1940s was driven by the military’s need for high strength, lightweight materials. Fiber reinforcements were introduced in aircraft the 1960s in order to strengthen the materials that were already being used in manufacturing. Composite materials have high strength-to-weight ratios – this means that they are stronger and stiffer than traditional metallic parts, but with a lower overall structural weight.
In addition to weight efficiencies, there are several advantages to using composite materials over traditional metallic materials in aerospace parts. Composite materials can easily be molded into shapes in order to conform to aerodynamic or ergonomic profiles. And while traditional metals are susceptible to fatigue and corrosion, composite materials are non-corrosive, and a vibration damping composite material will reduce vibrations and help prevent fatigue.
Transitioning from existing materials to new technologies will never happen overnight—there are many potential applications for composite materials, and finding the best application takes time, money and manufacturing changes in order to transition from one process to another.
However, using every technology possible in order to not only keep up with the market, but innovate beyond what is currently available will allow aerospace manufacturers to step above the competition.
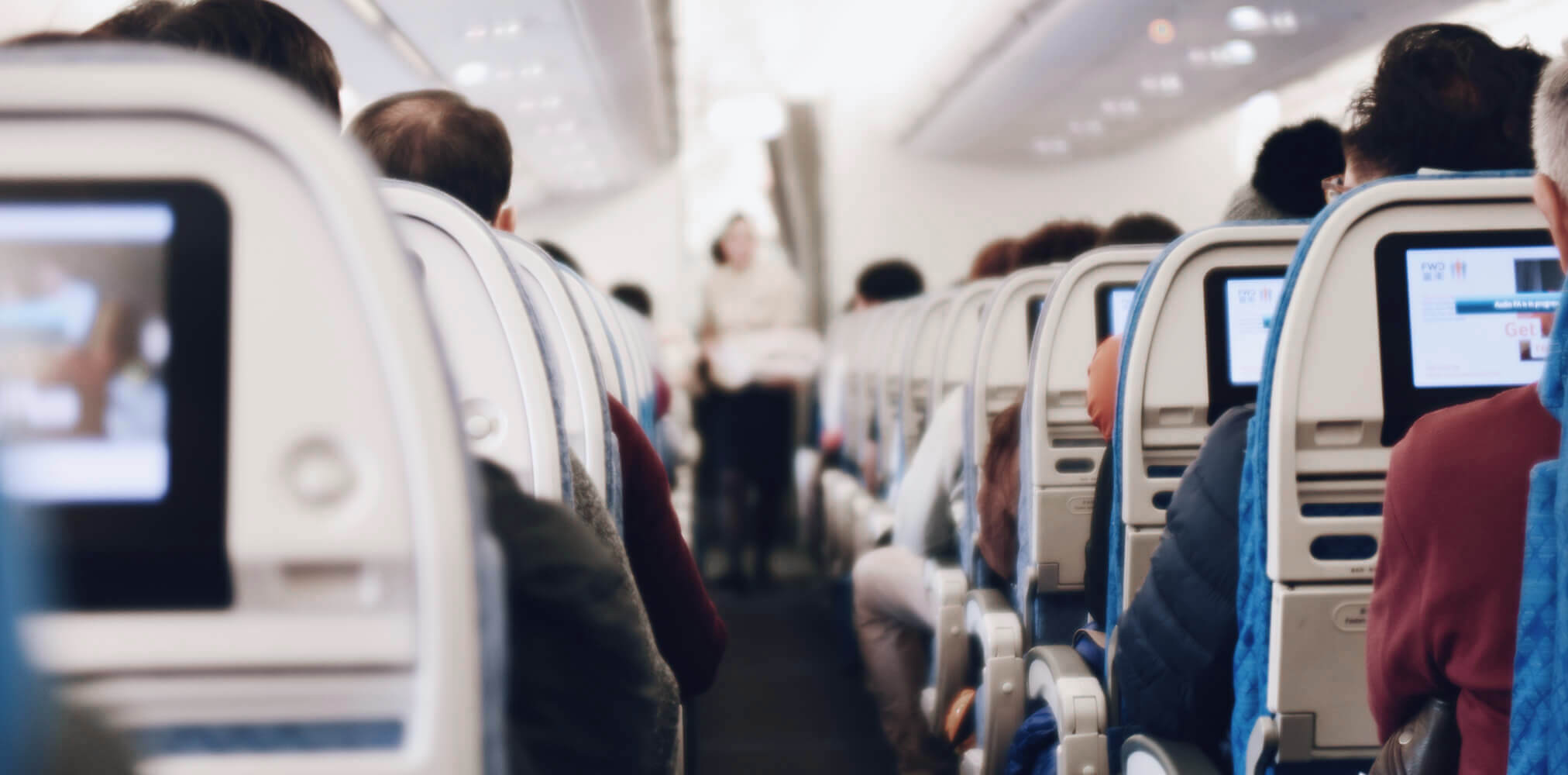
Vibration Damping and Opportunities for Innovation
As aircrafts become larger, more frequently traveled and fuller, it’s imperative to ensure a high level of comfort for passengers.
There are certain aircraft parts and areas in which multi-functional composite materials can be most effective—for example, adding a vibration damping composite material to laminated interior cover panels can help with passenger experience in airplanes, reducing vibrations while keeping a familiar and strong structure. So while some aspects that are traditionally metallic are likely to stay the same, including the skin and some structural elements, there are many opportunities to incorporate advanced composite material solutions throughout the aircraft; without significantly impacting the manufacturing and production process.
Historically, aircraft cabin quieting solutions have tended to be heavy and difficult to implement—using specialty engineered lightweight composites can help reduce dynamic mobility and structure-borne noise levels with minimal parasitic mass added. This can be extremely beneficial in longer nonstop and red-eye flights during which passengers are more likely to sleep and want minimal noise and vibrations to disrupt them.
Reducing as much weight as possible can also have a positive impact on fuel efficiency.
Boeing introduced its 787 Dreamliner in 2011, which was made using a 50/50 combination of traditional materials and composite materials. Along with improved aerodynamics and engine improvements, the lightweight composite materials contributed to a 25% improvement in fuel efficiency as compared to other previous designs.
Flying Above the Competition
While the use of composite materials started primarily in military aircraft manufacturing, specialty engineered vibration damping composite materials will likely play a larger role in the future of commercial aerospace manufacturing where enhanced passenger experience is a design goal. As airlines look to make their fleets lighter, more efficient and more comfortable for their passengers, they will look to the areas that they have not yet innovated and in which they can improve.
As with any innovation, there are several factors to consider when implementing a new technology. The time required to implement new materials, the changing manufacturing process and the cost of upgrading to vibration damping composite materials can all add up. While the cost of innovation is clearly a factor in an aerospace market with fluctuating demand, the bar has been raised by aerospace manufacturers in recent years in terms of innovation, and it’s imperative to not only keep up with what the industry holds as a baseline requirement, but to excel beyond it and look to the future.
The benefits of using lightweight composite materials in aircrafts are undeniable – from lightweighting to high impact resistance to noise reduction. Technology improvements such as implementation of multi-functional composites will help you to stand out from a crowded aerospace manufacturing field, especially when your improvements serve to better the flying experience.